Меню
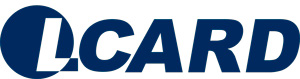
+7 (495) 785-95-25
sale@lcard.ru
sale@lcard.ru
Адрес: 117105, Москва, Варшавское шоссе, д. 5, корп. 4
Многоканальный телефон:
+7 (495) 785-95-25
Отдел продаж: sale@lcard.ru
Техническая поддержка: support@lcard.ru
Время работы: с 9-00 до 19-00 мск